

Pre-Order the New Raise 3D SLS System
Powder sintering tech for high-precision industrial parts

Advance beyond prototypes
Generate ultra fast models for concept & testing or rapidly deploy custom phygital assemblies directly to customers.

Transform Your Design Process with ANSYS Discovery
From concept to validation—experience real-time simulation and powerful modeling in one intuitive platform
1
/
of
3
Solid Technologies
AXTRA3D Lumia X1 SLA 3D Printer
9.8 x 5.5 x 19.6in Envelope
Hybrid PhotoSynthesis (HPS): This technology integrates a Laser and DLP system to simultaneously image internal and external structures.
Talk to a 3D Printing Expert
888-762-8441 (9AM-5PM EST)
Share
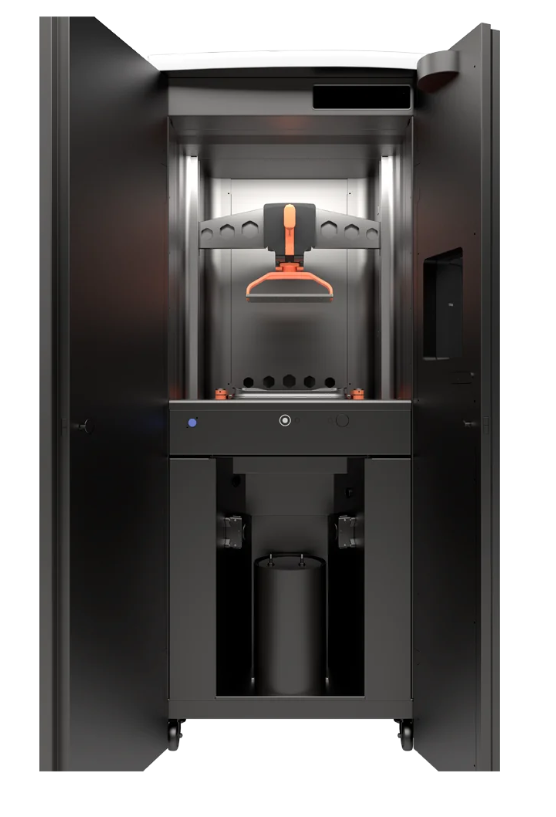
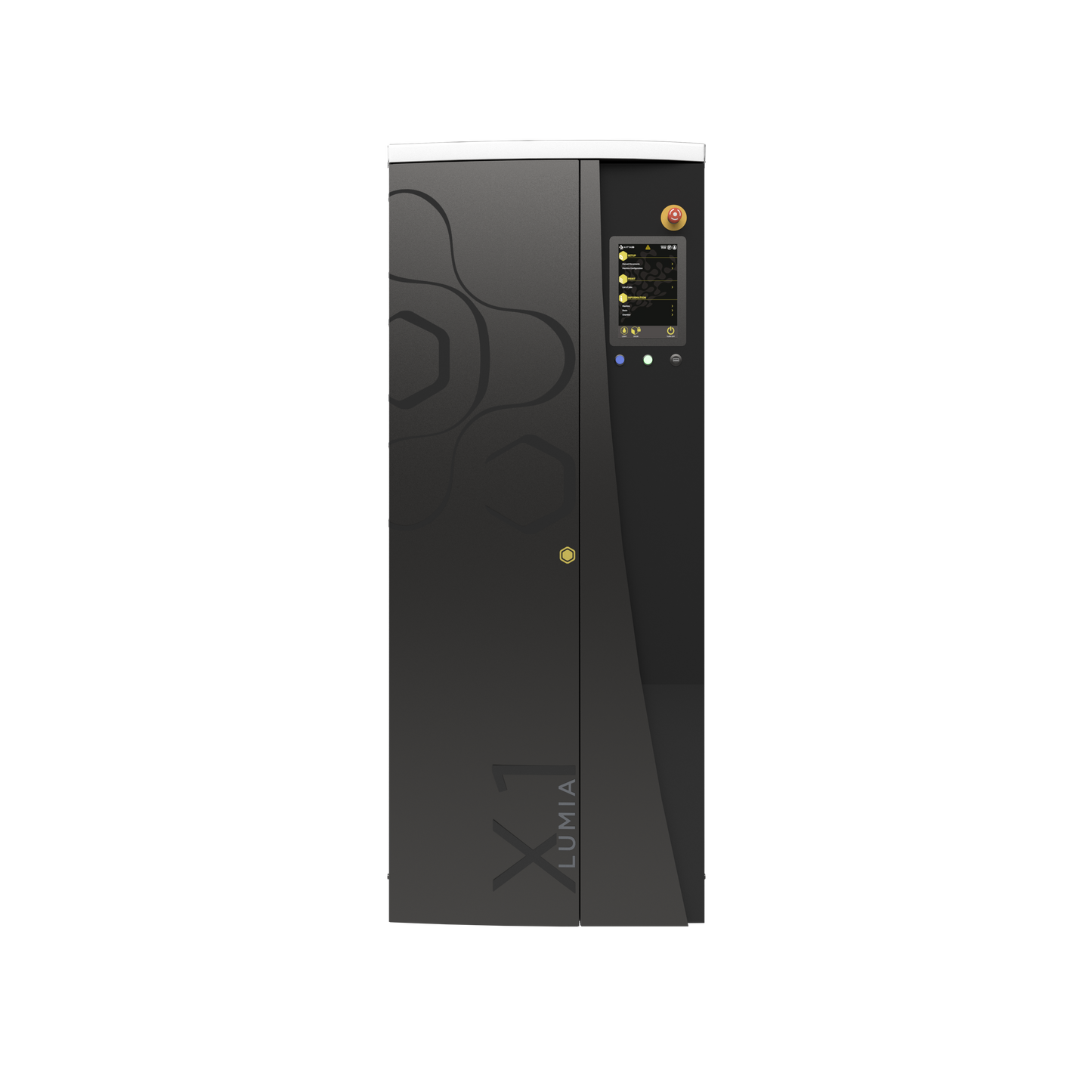
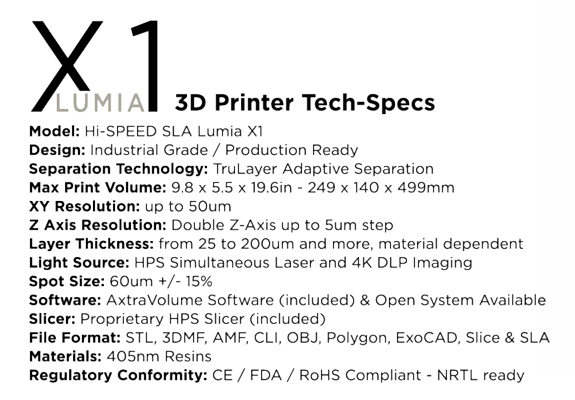
Filament, Resin, Metal, and SLS Platforms
-
Raise3D RMS220 Series Pre-order Standard Package
Regular price $39,998.00Regular priceUnit price / per -
Raise3D RMS220 3D Printer Pre-Order
Regular price $29,999.00Regular priceUnit price / per -
Raise3D RMF500 3D Printer
Regular price $69,999.00Regular priceUnit price / per -
Raise3D Pro3 Plus HS
Regular price $7,599.00Regular priceUnit price / per -
Raise3D Pro3 Hyper Speed Package
Regular price $4,999.00Regular priceUnit price / per -
Raise3D Pro3 HS
Regular price $5,599.00Regular priceUnit price / per -
Raise3D Pro3 3D Printer
Regular price $4,599.00Regular priceUnit price / per -
Raise3D Pro2 Plus 3D Printer
Regular price $2,999.00Regular priceUnit price / per -
Raise3D Forge1 3D Printer
Regular price $9,999.00Regular priceUnit price / per -
Raise3D E2CF 3D Printer
Regular price $3,999.00Regular priceUnit price / per -
Raise3D E2 3D Printer
Regular price $2,999.00Regular priceUnit price / per -
Raise3D DF2 Complete Package
Regular price $3,999.00Regular priceUnit price / per -
Raise3D DF2 Basic Package
Regular price $2,499.00Regular priceUnit price / per -
Raise3D DF Wash Bundle
Regular price $1,299.00Regular priceUnit price / per -
Raise3D DF Cure
Regular price $1,699.00Regular priceUnit price / per -
Raise3D Build Unit 220
Regular price $4,999.00Regular priceUnit price / per
1
/
of
16